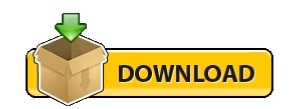
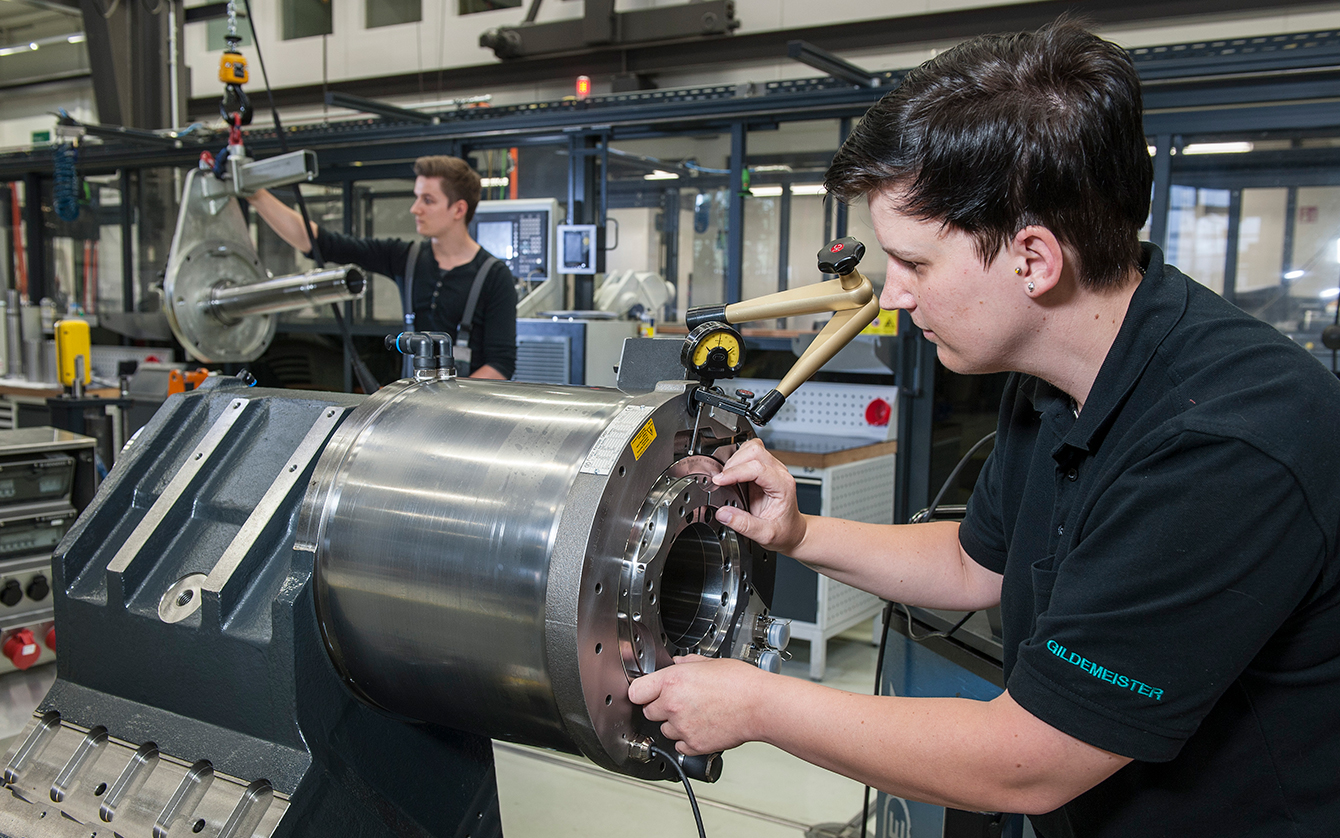
As most of those test hours are done during off hours, the Messenger software is key to help keep the staff abreast of issues arising during the testing process.
DMG MORI DAVIS JOBS MANUAL
Those measurements are also moved into the digital system and allow for immediate correction from the management staff.Īs Piner guided visitors through the manual production process, he noted each machine runs for at least 100 hours, including at least a circle-diamond-square test cut. There are also two measurement stations, including one for pieces up to 16 ˈ (4.88 m), that are accurate to 0.5 µm. The computer allows for quick reference and search of those manuals.
DMG MORI DAVIS JOBS MANUALS
Piner said the computer kiosks also allow for digitized manuals, as each employee is responsible for sizable chunks of manuals up to 1,000 pages long. The kiosks allow employees and management alike to keep track of process times and issues, allowing each party to identify bottlenecks and work toward continuous improvement. The kiosks and cockpit are connected through DMG Mori’s Messenger software.Īttendees toured the DMG Mori machine tool manufacturing facility at DMG Mori’s Davis, Calif. One stop on the tour was a hand scraping station, where an employee spoke of his lengthy training in Japan-where DMG Mori is headquartered-and explained that this process still can’t be automated because of the ultra-precise nature of this operation.Īt each assembly station throughout the factory floor are kiosks with large monitors where staff can input their process into computers that can also be viewed by management at the “factory cockpit,” a station with four TV screens tracking each machine’s progress. Each piece has a QR code that is scanned at each stage. The easiest integration is the inventory control system that keeps track of all 3,000 plus pieces, from receiving to warehouse to kitting to assembly. While the assembly may still be manual, the company is doing its best to incorporate computer assistance wherever possible. Digital Factory-Quality Through AssemblyĭMG Mori’s General Manager Zach Piner guided visitors through a half of the factory that is still manual, where highly skilled workers build large machine tools consisting of more than 3,000 parts by hand. The sessions, provided DMG Mori employees, discussed the integration of software and automation throughout the factory as well as at the end users’ plants. The two-day event offered a variety of guests the ability to tour the state-of-the-art factory and learn about the DMG Mori’s products and production processes through a series of seminars, such as “Digital Factory - Quality Through Assembly,” “Myth: Automation is Only for High Volume,” and “Digital Factory - Machine and Tool Monitoring.” On a blustery early October day, hundreds of customers and employees gathered at DMG Mori’s Davis, Calif., machine tool plant for the company’s “Manufacturing Days.” Attendees at Manufacturing Days take a close look at the DMC 340 from DMG Mori.
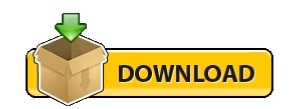